Click
on the picture for the video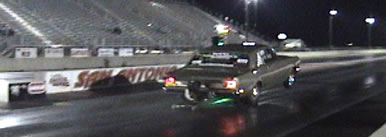
August 16, 2006: The
Falcon has gone through many changes since October of '05. We found
out the heads were not as good as we thought they were so we went with
a newer style Yates head to get the flow numbers we are looking
for. We changed the intake manifold to a Roush ported Motorsport manifold
to work with the new heads. The camshaft we had was way too small and was not designed to work with nitrous, so we went to Tony Bischoff at BES Racing Engines to help us match a cam to the new heads. We also went with new pistons with the top ring land moved down and lateral gas ported for nitrous. We have added a high speed data logger from RPM Performance, Inc. to help with accurate tuning and to get the most out of our combination. We decided to plumb the second stage on the Speedtech Diffuser plate as well, giving us a total of 3 stages of nitrous.
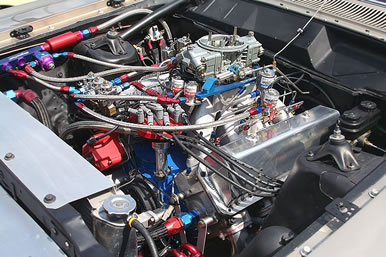
photo courtesy of Nitroart.com
September 2006: We went back
to Houston for the Maximum Impact race. We had difficulty tuning
multiple stages so we ran the fogger by itself and qualified #8 out of
16 cars with a 5.67. The pairing was done on a sportsman laddder
so we ended up with the #1 qualifier in the first round. Unfortunately
we lost in the first round to a 4.98.
During the last pass of the evening, we noticed the 2-3 shift was starting to show a significant flair. We pulled the transmission out to inspect the high gear clutches, only to find they were basically gone again. At this point, we decided to switch to an ATI Superglide; this is the baddest glide on the market.
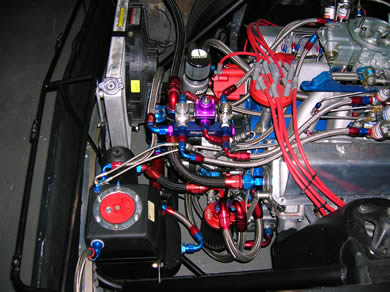
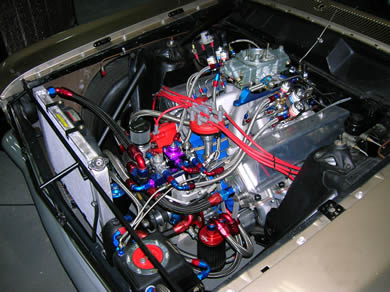
October - December 2006: We decided to remove the plate system and add another fogger to allow for individual cylinder tuning on both stages. To avoid any future fuel delivery problems, we decided to move the fuel system to the front of the car so the fuel would move in the direction the car is moving in. We also added bleeds to the nitrous side of the fuel system to keep the fuel pressure more consistent and prevent regulator creep when the solenoids are not open.
In an effort to reduce front end weight, we decided to make tubular chromoly upper and lower control arms for the front end. This allowed us to use heim joints on all of the front suspension pivot points and almost infinite front end adjustment. We are able to achieve over 8 degrees of caster in the alignment now. The stock front bumper was also changed to a much lighter fiberglass bumper. We also removed the big block radiator and changed to a smaller one.
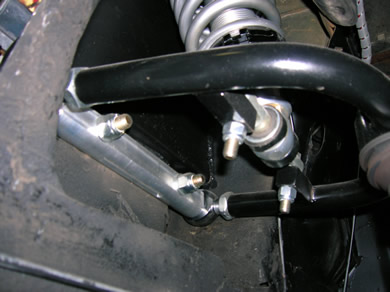
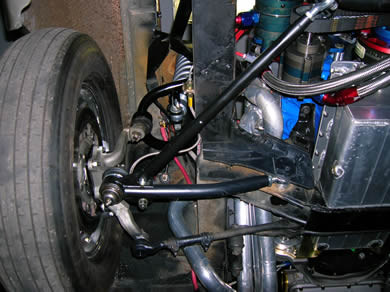
January 2007: To prevent air from entering the engine compartment, we made a form-fit fiberglass insert to attach to the back of the grill. We also made a filler panel to go between the grill and the bumper splash guard to block air and make it go around the car.
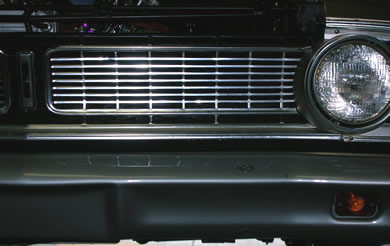
February - May 2007: While we were down for the winter, we decided to update the chassis to SFI 25.5 certification. We also changed the rear track locator to a more precise wishbone we well as adding a rear anti-roll bar to keep the Falcon straight and level during launch. Part of the chassis update included a larger diameter transmission cross member so we made sure we tucked the cross member up close to the floor to allow us to run mufflers when we want to. We also removed the factory steering column and went to an aftermarket one to reduce weight.
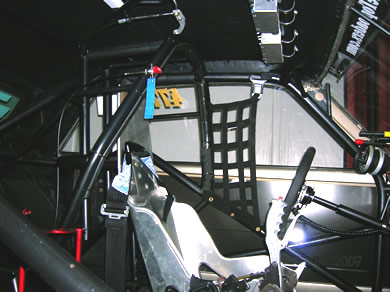
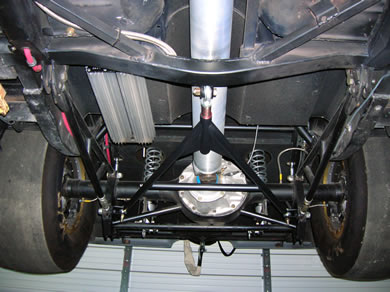
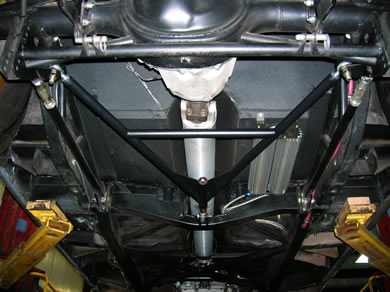
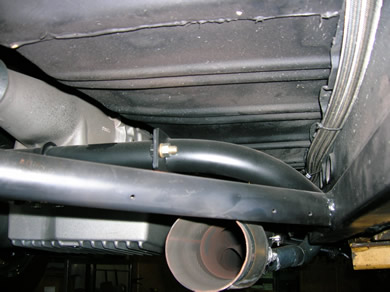
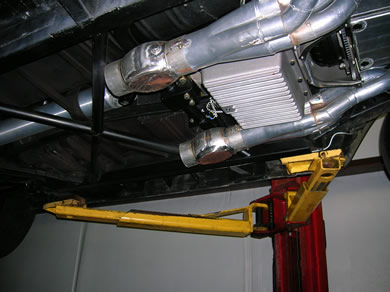
June 2007: We had to make a new driveshaft when we went to the glide so we upgraded to a 4" aluminum driveshaft with 1350 u-joints and a Strange billet yoke for our roller tail housing.